ESG
Environment
Environment
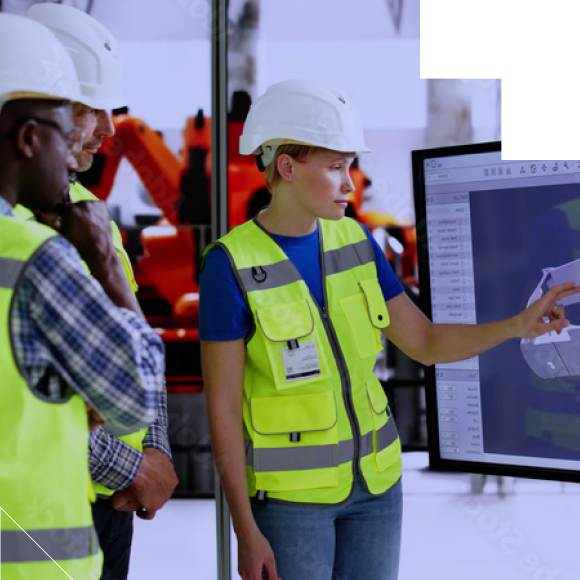
Taking a responsible approach to managing our impact on the natural environment aligns with our core social and ethical values and helps to build social and relationship capital with customers, communities and regulators. Failure to adequately manage our environmental impacts risks reputational damage, fines and the loss of our social licence to operate.
- Environmental issues are monitored by our social and ethics committee (of which our CEO is a member), which then reports to the board. At operational level, environmental management forms part of the safety, health and environment (SHE) function.
- We believe that formal measurable and auditable systems are of utmost importance to allow objective measurement of performance against world class standards. All of the group’s subsidiaries are accredited under ISO 14001 (environmental management) and are in the process of implementing ISO 50001 (energy management).
Climate change
Metair is cognisant of the United Nations Framework Convention on Climate Change (UNFCCC) Paris Agreement which focuses on mitigation of GHG emissions and climate change adaptation. The agreement aims to ensure that the increase in global average temperature remains below 2°C above pre-industrial levels to reduce the risks and impacts of climate change. We recognise that the consequences of climate change could have a significant impact on the group’s activities. We monitor our greenhouse gas (GHG) emissions and set targets to ensure that the group’s contribution to GHG emissions is mitigated and that we adapt to the changing climate and environmental conditions.
Potential direct and indirect impacts of climate change identified by our subsidiaries include:
- supply chain disruptions and increased cost of transport;
- water constraints directly affecting our activities, and affecting households and workers in the area;
- reduction or disruption to production due to extreme weather events;
- increased temperatures leading to increased heat stress and dehydration in the workforce and increased cooling costs at production facilities;
- the shift to electric vehicles driving increased demand for lithium-ion battery technology and reduced demand for lead acid batteries; and
- rising costs due to carbon tax.
Metair reports in terms of the Task Force for Climate-Related Financial Disclosure (TCFD) principles and guidelines. Metair participated in the 2022 CDP Climate Change project and achieved a B CDP score (2021: B), indicating that we are currently at a “Management” level regarding our approach to climate change. This score places us above the averages for global powered machinery companies (D), African companies (C) and the global average for all companies (C).
Carbon Footprint
Metair’s total carbon footprint increased by 0.3% to 614 258 tCO2e in 2022 (2021: 612 616 tCO2e) as increased production at Mutlu Aku offset closures and short-time at several South African subsidiaries due to the floods. Scope 3 emissions increased by 1%. There were some adjustments to the 2021 Scope 3 emissions report to account for FNB’s recycled lead purchased, Hesto’s water purchased, Rombat’s recycled lead and ATE’s recycled lead.
Electricity consumption
Electricity is the primary source of energy used at our operations, as well as various fuels, including petrol, diesel and gases
We monitor electricity use as a key input in our manufacturing processes and an expense. All operations have implemented the ISO 50001 energy management system, which requires that companies demonstrate improved energy efficiency.
Energy efficiency initiatives include ongoing training and awareness, increasing natural light and switching to energy efficient lighting, switching off equipment and lights when not in use, insulating equipment, energy monitoring to identify areas for improvement, reducing scrap, decommissioning underused machinery or facilities, installing variable speed drives and replacing pumps, fans and motors with more energy efficient alternatives. New machinery replacing old machines in the maintenance cycle is generally more energy efficient.
Metair is also investigating opportunities for energy storage solutions for alternative power generation, including solar support energy systems.
Waste management
We reuse or recycle wherever possible. Waste separation programmes and ongoing training and awareness initiatives emphasise the importance of proper waste segregation at source. Waste that cannot be reused or recycled is disposed of in a responsible manner and in compliance with the relevant legislation. Hazardous waste is disposed of using registered disposal companies.
Scrap reduction targets are set at each subsidiary for primary and secondary materials to minimise waste from production processes to improve manufacturing efficiency. These targets are supported by dedicated scrap programmes, close analysis and regular interrogation of the root causes of excess scrap, as well as switching to efficient machinery and equipment.
Batteries and recycling
Lead is included in the list of substance banned in Europe by EU directive 2000/53/EC. OEMs are required to limit these substances in new vehicles and ensure that they are responsibly managed throughout the vehicle lifecycle. Our goal is to reduce the amount of lead used in our batteries without affecting performance. Lead-acid batteries are nearly 100% recyclable and all of our battery manufacturing facilities have recycling plants on site. Recycled lead uses around a third of the energy needed to produce virgin lead and is cheaper to access. Lead recycling helps to manage costs, secures supply of a critical input and also ensures that lead is managed responsibly through the battery lifecycle. The recycling plants extract lead from battery grids and terminals, refine and blend it to produce high-quality lead alloys for new batteries. The yield on lead recycling and plastic recycling percentage are tracked as measurement criteria for waste management. Acid from the batteries is neutralised and processed through an effluent plant and the plastic from the battery casings is recycled into new battery casings.
Water consumption
We recognise that water is a precious resource and our focus on improving manufacturing efficiencies includes an emphasis on reducing water consumption, increasing water efficiencies and recycling process water where possible. Fresh water is withdrawn from municipal sources and boreholes. Municipal water use is measured from municipal meter readings and corroborated by readings from internal meters where these have been installed. Borehole water is measured through internal meter readings. Water saving initiatives include training and awareness, water use monitoring, leak identification and repair, switching off underused cooling equipment, installing water saving taps, rainwater harvesting and reverse osmosis water purification plants at Smiths Manufacturing and Lumotech to recycle and recover process water.
The battery formation process uses large quantities of water and the businesses in the Energy Storage Vertical account for 79% of total group withdrawal.
Environmental impacts
Metair aims to ensure that all components manufactured across the group have a positive life-cycle and end-of-life impact on the environment.
Retail customers buying new automotive batteries are incentivised to return old batteries to bring the lead back into the recycling process. However, our ability to reclaim products or packaging from end users in our automotive components business is limited given that these end up as components in vehicles that may be manufactured in, or exported to, other countries. We aim to control and eliminate as far as possible the use of Substances of Concern (SoC) in our products. We closely monitor the chemical composition of our products and submit full material declarations for all the components we manufacture in line with the International Material Data System.
Environmental compliance and impact
Metair’s aims to comply with or exceed the requirements of current environmental legislation and codes of practice in all countries of operation. The Code of Ethics emphasises compliance with safety, health and environmental (SHE) regulations as one of its core pillars and environmental compliance is integrated into our operating practices and environmental management systems.
The material makeup and environmental impact of our products and their constituents are subject to the strict environmental laws in Europe and Japan that apply to our OEM customers, which include regulations to reduce waste arising from end-of-life vehicles.
